Everyone knows the saying “electrician is never touched by the current” or “electricity doesn’t’ kill an electric guy” and how is it with automation specialists? It happens that sometimes we have to bury ourselves in the wires during modernizing some kind of control system. Sometimes we have to roll up our sleeves and take care of comprehensive prefabrication of control cabinets.
I am certain about one thing, each of us has a relationship with electricity that “doesn’t kill the electric guy”. Here the question arises: is the automation specialist also part of electrician? Because in total, the automation specialist must have also knowledge about electricity, right? Just to be able to create electrical installations in control systems. I am not convinced to it because in my case the saying “electrician is never touched by the current” did not work… several times. I will cite two situations.
THE LAST ONE TURNS OFF THE LIGHT
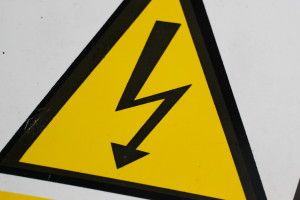
The general rule of modernization of existing control systems is that all work, if possible, should take place when the proper power supply is turned off. If it is not possible, due to the need for continuous operation of the facility, then you can work under voltage. Of course, only when you meet the relevant requirements. In this case, the facility – water purification station – was in the large part of the city, which we retrofitted with additional system of remote communication with other facilities.
Due to the potential downtime of this facility, which nobody even wanted to heat about, all the modernizations were carried out at night. In one of the existing control cabinets I had to add several relays exchanging signal with a new telemetry cabinet. Many of you would say that it’s a job for an electrician rather than automation specialist. I say “sometimes you have to commit yourself”.
The mat under the feet – check. The safety footwear – check. Insulated tools – check. Signatures – check. Supervision, papers – all check. Everything is correct. We can start working. Initially I assess the location of relays, I pay attention to the exposed elements under voltage, for example – on the main switch on the door of the control cabinet. I protects everything that’s possible and start the installation. The relays latch onto the DIN rail, the covers from the cable trays ‘jump off’ with a characteristic sound and I start to pull in previously prepared cables to the new cabinet. As the automation specialists say I ‘sew’ a control cabinet. And although I tried as much as I could and although I was protected by a team member – older than me and more experienced than me – and although the saying “electrician is never touched by the current”, during this work I was… touched.
What happened? After all, I checked and secured the work station and I was very cautious – at least I thought so. I was sure that I had not touched any exposed elements under voltage or any wire from any device. So I started to investigate the place of incident, this time taking necessary precautions. As it turned out, in the wire tray between a bunch of electrical wires one was hidden, quite deeply, insulated and clamped with a bushing wire under the voltage of 230V. Where did he get there from? Either he was there from the beginning or, this seems more likely to me, was the remnant of some previous modernization. Someone just didn’t want to remove the whole wire so he decided to cram it in existing wires…
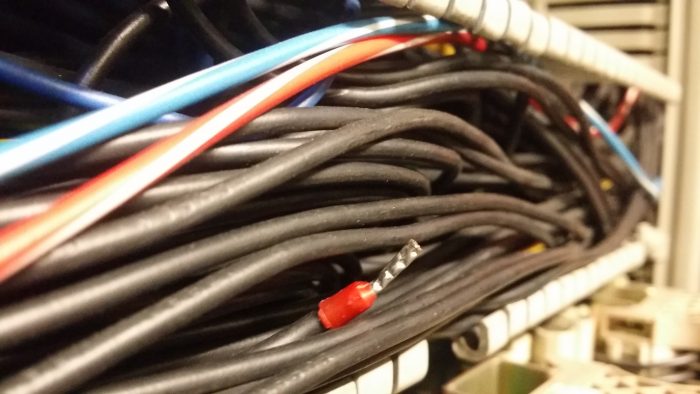
Lesson 1 – limited trust to potential predecessors.
Lesson 2 – electrocution hurts.
NIGHT SHIFTS
The second case also took place in the water facility. It was water-pumping room with five pumps on board that kept the water pressure constant at the outlet. In short, thanks to the pump-room we have constant water pressure in out taps – in homes and apartments. The customer wished to have a detailed analysis of the work parameters of each engine, using analyzers in pairs with current transformers on each phase. In addition, the data should be remotely sent to the control room. The order specification in this case was not the subject to discussion, our client is the king, so the order should be carried out. Five motors + three phases = fifteen current transformers to be placed in existing control cabinet – and there was not enough space for that.
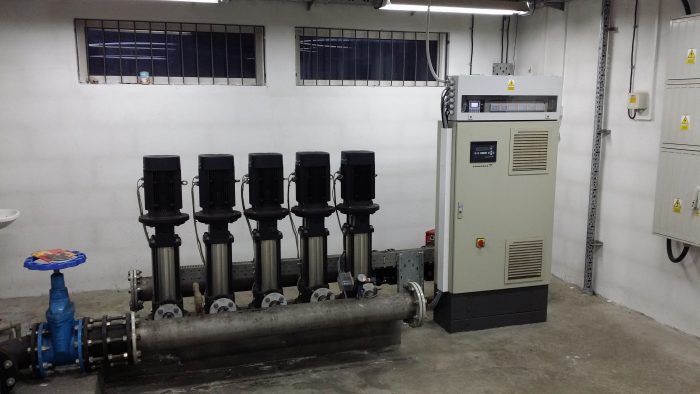
After reorganization of several existing elements, it was possible to obtain free space for the transformers, and the analyzers with the remaining elements were in the additional cabinet. The works also took place in the night, not to cause a lack of water during the day. In the night two working pumps were enough to maintain the set pressure. The three remaining pumps could be disconnected from the power supply and we could install the current transformers. This entailed with the extension of each phase and passing it through each transformer. More less during the 13th phase, I experienced a strong electrocution… I had to walk it off. It turned out later that I disconnected not the motor I needed and started modernization on the currently working pump. Ouch!
Lesson 3 – before touching insulated electrical elements, always make sure that they are not electrified.
Lesson 4 – always.