There are growing concerns about environmental problems due to the increase in the average temperature around the globe, such as abnormal climate change, decline in crop productivity, impact on ecosystems, and habitat change resulting from rising sea levels. Energy saving actions are urgently needed to prevent global warming (to reduce CO2) emissions.
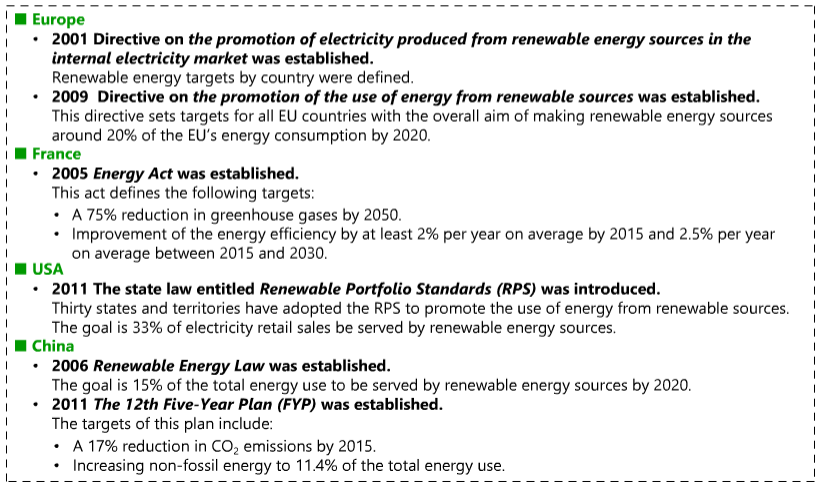
The number of devices powered by electricity is almost unimaginably large. Electric motors can be found in everyday life, literally everywhere. From vacuum cleaners, air conditioners through moving stairs, elevators to electric cars. There are even more of them in the industry! Machine tools, conveyors, production machines. It is easy to guess that electric motors make up a large percentage of the world’s electricity consumption.
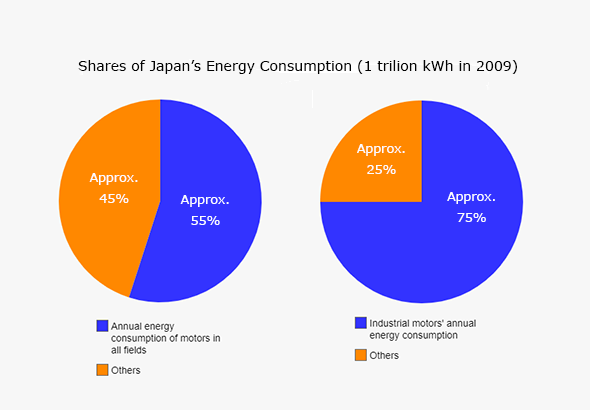
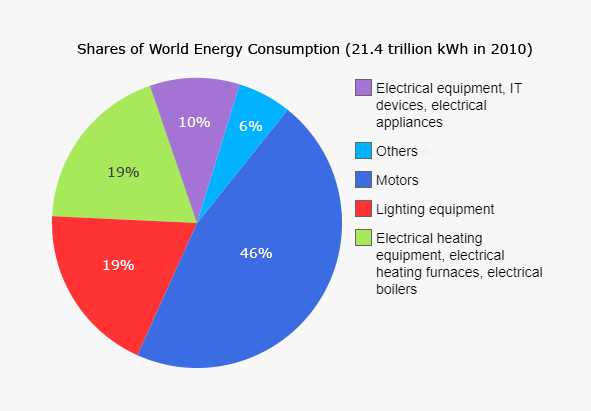
On a global scale, it is 46% (for 2010)! In Japan itself, taking into account all areas of the economy, the share is 55%, and considering only industry, it grows to 75%. To better illustrate this, note that the remaining percentages include the rest of the devices powered by electricity: heating devices (electric heaters, electric stoves, boilers and kettles, electric cookers), electronic (including computers, televisions, industrial devices, drivers), lighting, etc. Imagine one more thing. If so, all currently used engines should be replaced with energy-saving engines, how huge the savings of electricity would be!
So the question arises: how can you reduce the energy consumption of electric drives? One of the ideas may be the use of frequency converters. Another application of high efficiency motors.
Do you understand how this can help you to save energy? I will try to explain this on the basis of Mitsubishi Electric’s FR-F800 and FR-F700PJ frequency converters and the Superline Premium SF-PR and IPM series.
The basics of energy saving using frequency converters
Why can a motor powered by a frequency converter save energy? A simple example is a blower. When powered directly from the grid, the engine speed does not change very much even when the load changes. Therefore, to control the volume of air pumped, install a shutter plate called a damper. This solution introduces energy losses and requires the use of additional mechanical components and an external control system.
What will change the introduction of a frequency converter to control the motor speed for this system? First of all, the need to use a throttle, which as a mechanical element may cause failures, eg by blocking in one position, will be eliminated. The control of its technical condition will also not be required. The inverter will now be the external control system.
When the motor is powered by a frequency converter at medium speed, the voltage is reduced in proportion to the motor speed, regardless of the current flow, which saves energy. One can be tempted to say that virtually any application, feeding a variable speed motor from a frequency converter, will reduce energy consumption.
The torque load characteristics are also important for a given application. Depending on the object, the load torque can be constant or change when the motor speed changes.
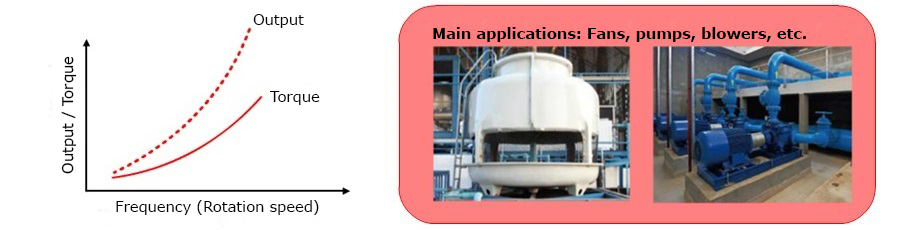
Useful energy-saving functions
The FR-F800 series inverters are easy and safe to use, and support a wide range of energy-saving applications, offering a variety of functions ideal for fans and pumps.The FR-F700PJ series are ideal for fans and pumps enable energy saving. The biult-in filter pack achieves a compact design with reduced wiring.
A newly developed advanced optimum excitation control delives a large starting torque while maintaining the same motor efficiency as under the conventional optimum excitation control. Rapid acceleration is enabled without troublesome parameter settings (e.g. torque boost, acceleration/deceleration time). Energy-saving operation with maximum motor efficiency is possible during operation at a constant speed. The offline auto tuning function to measure circuit constants of the motor enables optomal operation of motors even when motor constants vary, when a motor of other manufacrurers is used, or when the wiring distance is long. Since the 24VDC external power supply allows the control circuit to operate independently , parameter setting and communication are possible aven after turning off the main power.
The inverter coolinf fan can be controlled in response to changes in the temperature of the inverter cooling fins. Since signals can be ouput in response to the operation of the inverter cooling fan, a fan installed on a panel can be operated in synchronization with the inverter cooling fan. Unnecessary energy consumption while the motor is not in service can be reduced. The energy saving effect can be checked using an operation panel, output terminal or network.
High-efficiency motor regulations
Large energy savings can be achieved by improving the efficiency of motors, or by using motors combined with inverters. The introduction of regulations for mandatory use of high-efficiency motors is being promoted worldwide due to the increasing awareness of the need for energy saving to prevent global warming.
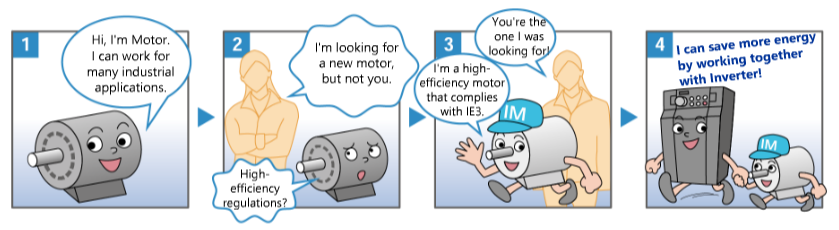
IE is the abbreviation for International Efficiency Standard Level and it defines the international standards for motor efficiency. The global trend towards improving efficiency is accompanied by rising demand for high-efficiency motors worldwide, it was necessary to integrate the motor efficiency standards that had been uniquely defined according to indicidual countries. In October 2008, the IEC established the international standard IEC 60034-30 (Efficiency classes for single-speed squirrel-cage induction motors). This standard defined the IE codes. The IE codes includes four classes.
Superline premium series SF-PR motors
The SF-PR motor conforming to Japan’s unique Top Runner Program Standards (equivalent to IE3) achieves 6% higher energy efficiency that rhe SF-JR standard motor (7.5 kW). Energy-saving operation can reduce electricity charges, reducing running costs.
With a 6% increase in efficiency Approx. 75,000 yen/year in electricity charges can be saved. In 100 motors are used, Approx. 7.5 million per can be saved per year.
The initial cost of introducing a high-efficiency motor (motor SF-PR) is expensive; however, its high frequency and reduced power consumptions will realize more cost-effective operation after the first two years compared to using a commercial power supplye (damper control).
Compatibility in motor installation deimensions (frame number) between the SF-PR series and the SF-JR series makes it easy toi replace a motor.
Energy saving with inverter and IPM motor
IPM is the abreviation for Interior Permanent Magnet. IPM motors with permanent magnets embedded in the rotor have higher efficiency that induction motors, and meet the customers’ needs for further energy saving.
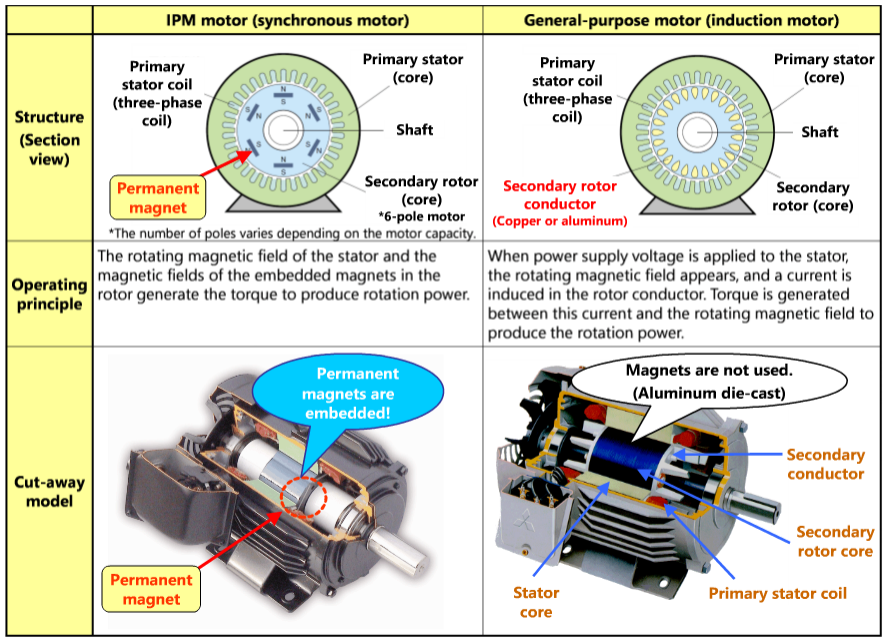
The rotating magnetic field of the stator and the magnetic field of the embedded magnets in the rotor generate the torque to produce rotation power. Since no current flows through the rotor side (secondary side), there is no secondary copper loss. This reduces the energy loss. Each of the following charts shows the breakdown of the motor internal loss.
Reduction of internal loss in the amount of 60% for the 22kW motor will directly change into an improvement in the efficiency of the motor, because as it is known efficiency is the ratio of the output energy to the input energy (sum of the output energy and losses). Even considering the situation in which the IPM motor works in conjunction with the inverter at rated speed, the total generated loss (inverter and engine) are still lower than with a standard induction motor supplied directly from the grid.
Returning to the example application in the building, you can observe a further increase in savings:
The increase in saving is much bigger in the even when compared to already highly-efficient SF-PR series motors. The initial installation costs are slightly higher (10%) than the costs of SF-PR installing . When using the IPM motor, the installation cost will be payed back after three years (compared to the standard motor), and after five it will be more profitable than the installation with the SF-PR series motors. Longer intervals, e.g. replacement of bearings, will bring additional profits in the form of time and money saved.
SUMMARY
There are many ways of saving and the chioce of the appropriate, optimal way usually depends on many factors. For production companies, where a large number of constantly operating electric drives are used, energy-saving solutions can bring profits. But in the cases where the device works for a short period of time or is used sporadically, investing in advanced technologies may miss the goal. Therefore, knowing the degree of use of given machines and the conditions of their work, the analysis should evaluate the cost-effectiveness of investments in new drive technologies and the time of reimbursement of their costs, and only then start their implementation.
Author: Paweł Z.