I think that most of us have heard about industrial robots. In Poland, their use is still very small, so not everyone has to come into a contact with them. In this article I will present the basic dose of knowledge about industrial robots, and in the second part I will show examples of their practical application.
Industrial robots
Mass media and pop-culture present robots as humanoid devices from sci-fi story. However, these robots are not related to industrial robots. According to ISO, an industrial robot is a “programmable manipulation machine that can be controlled automatically and its operation can be programmed in three or more axes”. So it is a machine that can be programmed and operated automatically (without human intervention), has to have at least three motion axes, and operate on the principle of a human arm (manipulation machine).
Role of the robots
As we already know, a robot is a human-armed machine. Their work consists of moving these arms. Robotic movements can sometimes be difficult to predict, and programming and learning robots require the presence of people around. For this reason, there have been accidents in the past. Currently, work with industrial robots is assessed ad dangerous and requires operators to be trained. In some countries, the law requires from entrepreneurs the installation of security devices, such as fencing, to prevent people from approaching robots. Remember! If you work within the robot’s operation, always read the safety instructions and follow their guidelines.
Why are we using robots?
- They can be used to increase productivity – in contrast to people, they can work 24/7, in a constant and regular operation, and at high speed.
- They offer great versatility – they can remember programs for different models. They allow for an immediate change of the operation mode. They can be used to perform complex activities.
- You can easily update or change their position – the robot’s movements can be freely changed, adapting it to other activities. The robot can easily be moved to a different place in the factory or production hall.
- System startup is fast, and once learned robot can work for a long time without human interference.
- They help protect employees from accidents – although they may be a thread, they are well-configured to relieve people in the most dangerous jobs.
- They can be used to improve quality of the product – although man in the most complicates “machine”, he makes mistakes and is not repeatable. The robots can offer almost perfect repeatability and accuracy.
Structure of the robots
Industrial robot can be divided into several systems. These are:
- power system – a system that provides energy for the drives operation. Depending on the configuration of the robot’s drives and the type of energy source, these can be systems based on rectifiers or frequency converters,
- control system – PLC controller or another type of controller. Often there are also elements such as the operator panel, a special remote for manual control, various switches and buttons,
- kinematic unit – these are the moving elements of the robot. Industrial robots are kinematic units connected with each other in a row – i.e. parts of the mechanism, housings and drives. A kinematic unit is defines as a set of units. The movements of individual elements make up the final and desired movement of the gripper or other working part in space. Nowadays, combination of moving units, which can move each other in a linear or rotational way.
Types of industrial robots
Classifying of robots is becoming increasingly difficult, as they are becoming more and more advanced. Mostly robots are divided:
1. due to the way of operation:
- sequence robots – they go to the next steps after the current operation, according to previously set programs (sequence, conditions, etc.),
- playback robots – they constantly perform programmed, learned, saving activities,
- numerical control robots – they work on the basis of numerically read coordinates with a position in space,
- intelligent robots – they make independent decisions using artificial intelligence.
2. due to the construction:
- cartesian robots – equipped with an arm, which has three linear connectors. Each of them can only move in a straight line, according to Cartesian coordinates. They are very accurate and easy to control, but they have limited work space and they take up much space.
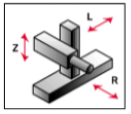
- cylindrical robots – equipped with an arm that has at least one rotary joint and one linear joint arranged according to cylindrical coordinates. They have more freedom of movement than Cartesian robots, but they cannot move in all directions. Thanks to the rotational connection they offer higher speeds at the ends of the arms.
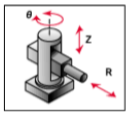
- arm robots – equipped with an arm that has at least three rotary joints. This allows for the greatest freedom of movements. Such a robot can set the gripper in any position in several ways. They allow to perform the most complex activities.
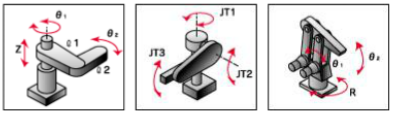
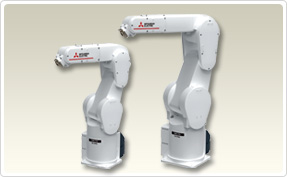
- SCARA robots – they have two rotary joints and one linear (the last one, the closest to the gripper). They are incredibly popular during working on a flat surface, various tables, palletizing, etc. They are characterized by the possibility of very quick action.
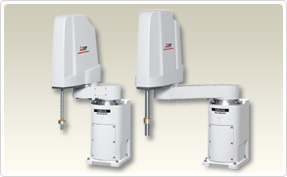
All robot types and detailed characteristics you will find on website MitsubishiElectric.com – Industrial Robots-MELFA.
Programming of robots
Programming languages for robots can differ between each other according to the manufacturer and configuration. The example below has been created in MELFA-BASIC language designed for Mitsubishi Electric robots.
To present how the robots are programmed, we will show you the example of palletizing operation.
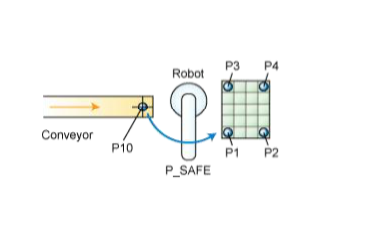
- P10 – position, where the workpiece is stopped on the conveyor,
- P-SAFE – safe point, where operations of robot start and end,
- P1, P2, P3, P4 – corners of the pallet,
- IN8 – signal given to the robot when a workpiece is at the stopping position,
- the distance of approach attachment/detachment point is 50 mm,
- the linear interpolation speed is 300 mm/s.
Here you can see the program, which set 20 workpieces on the pallet.