Not so long ago PLC controllers were the only viable solution for control needs in industry automation applications. Nowadays engineers have more choice – they can use industrial PCs, programs for controlling from the PCs level, and panel PCs imitating combination functions of PLC/HMI interface. Specialist, if he want to, he can build his own controller of the needs of specific application, basing on Raspberry Pi module.
There are still many important reasons to use a PLC, despite many control options entering the market. Here are only 10 out of many more reasons for using PLCs.
1. Peace of mind
Both PLCs and PCc have come a long way from their beginnings. There is a big difference between directions, in which these devices evolve, and this has a huge impact on their long term support. The managed evolution of the controllers means, that suppliers are able to provide support over long period of time, both in terms of software and hardware. This means, with Mitsubishi as the example, that we could take the program from a 20 year old FX PLC and import it into a brand new FX5U. the user is able to install the newest controller and make sure that the application will start working almost immediately. Doing the same with the use of a PC would be a little difficult. There are many branches of industry where the support level is not only desirable, but also required. For example, in water industry there is talk about the necessity of framework suppliers having to be able to assure support of control systems for up to 20 years. Of course, the control hardware will change over that time but PLC users won’t have to worry that their software will always be port into the latest controller.
2. Inherently robust and reliable
Modern industrial PCs provides a stable computing platform and it will be not true suggesting that they locked-up and crash with the regularity of a PC desktop. Nevertheless, such a PCs should not be treated equally to PLCs. A real-time operating system running alongside to Windows on a typical industrial PC is designed to provide the same level of reliability as the CPU control unit in a PLC. If PCs worked under completely isolated conditions, discussing reliability would probably be pointless. Well, no driver works in isolation – you need to connect peripherals, inputs / outputs and wire it. In addition, there are other devices to communicate with, and each of them requires separate drivers that need to be loaded into a PC. Can you be sure that the drivers for all these devices have been tested in terms of cooperation and that you can accurately verify their efficiency? It seems rather unlikely. Clashes can and do occur, and crisis situations can further deteriorate each time the drivers are updated.
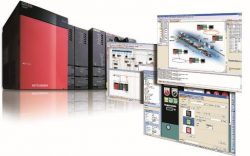
In this case, it is rather inevitable that an industrial PC will fail one day. What can this mean for the control process in a given plant? On the other hand, let’s think when we last heard about the need to restart the PLC after a software failure? Probably never …
3. Scalability
The best-selling PLCs, covering the widest range of applications, are controllers with 40 inputs / outputs or a smaller number. In the case of such applications, the PLC controller is a very advantageous solution, definitely better than a computer-based counterpart. At the same time, the same basic platform also offers the possibility of expanding to tens of thousands of I / O, and users can transfer control programs to larger controllers, using the same programming environment and completely modular hardware. The potential for individualization of the application found in controllers is huge, it offers numerous ways to expand PLC functionality, all without having to leave a common platform.
4. Programming
Nowadays, for every single engineer coming out of university who is able to structured text programming and for every engineer who is comfortable working in C or C++, there are probably a dozen of others who only want to use ladder logic, particularly at the lower I/O end of the application spectrum. The entire range of applications will include those that are initially small in size. Perhaps they were written in ladder language, but later they grow with the development of the application. This is possible due to the scalability of the PLC platform and the ability to write control programs in the structured text, and drag-and-drop functional software blocks that significantly ease the configuration process. Mitsubishi offers the C ++ programming option for PLCs, in other words it combines a flexible hardware platform with the programming function in a high-level language. Of course, the same programming options are available on the PC platform, however, the levels of modularity and scalability that characterize PLC software tools, PC platforms simply do not offer. The same also applies in principle to the hardware aspect.
5. Integration of other automation equipment
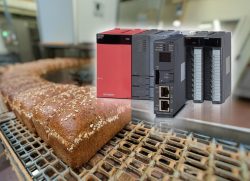
Many automation engineers never have to look for products outside the range offered by a single supplier, because manufacturers such as Mitsubishi are able to meet any demand – from human-machine interfaces, drives, servos, motion control devices, security systems and robots to low voltage power distribution products, power management meters and CNC systems. Because all of these devices were designed to work together, engineers can take advantage of the ‘plug and work’ function, which is the ability of devices to work right after they are connected. There are also automation suppliers on the market selling industrial PCs, claiming that they offer a substantially similar portfolio of devices, but certainly not many. For engineers, the challenge may be to go beyond the offer of the only supplier and integrate elements from other manufacturers. If we have the modern PLC, it is very easy to integrate devices from foreign manufacturers but can we say the same about integration on the PC platform? Can anyone guarantee that controllers for third-party modules will work? How much work will the configuration require? Let me ask you one more important question – will it be possible to rely on the guarantee of ongoing compatibility in the operational lifespan of the control platform?
6. Performance
In terms of computing power and performance, Moore’s law about doubling PCs performance applies to both PLCs and PCs. And that’s true that many of us forget that modern PLC controllers is a powerful computer. For example the latest Mitsubishi FX PLC is working 150 times faster than the previous ones. The huge potential of the latest PLC controllers can be seen only by paying attention to the speed of execution of instructions, which in the latest models is nanoseconds. Of course, we can try to ‘pimp’ a PC to offer a similar performance, but PLC controllers already have these parameters.
We also have to add that there is also increased bus speed and ability to synchronize many inputs and outputs in high speed systems, and that results in higher speed of control system response, and it’s hard to achieve outside the PLC environment.
7. Security
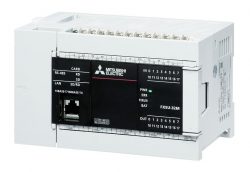
Powerful viruses, such as Stuxnet, make us realize that automation system have become targets of hacker attacks that implement hostile intensions to paralyze the work of large companies or the functioning of the public utilities. PCs characterized by the well-known operating system and inherent weakness of network operation may indicate shortcomings in the control system for a potential hacker. In contrast to PC operating systems, systems in PLC controllers are much less visible to the outside world, and this has been traditionally a protective layer against hostile intensions. This doesn’t mean that PLC manufacturers take this security for granted. For example, Mitsubishi has introduced the function of protecting programs with a password and assigning different levels of authority to different users. What’s more, you can enter further remote access preferences, e.g. grant access rights only to specific IP addresses, which will protect PLC software and the entire automation system in environments characterized by even in heavily networked applications.
8. Intellectual property
Analogically to the security problem, the worry of companies with global development departments or companies installing developed systems on other continents is ruthlessly copying control software by ruthless rivals and quickly developing it as a competitive, cheaper product. This topic applies to all system platforms, however PLC manufacturers have already taken serious steps to solve this problem. In the case of Mitsubishi products, the encrypted code embedded in the hardware and software can be programmed to be executed at the selected moment of time. This may mean that the system is open to programmers and installation specialists throughout the application’s start-up period, and then switches to a mode that protects the system from further interaction.
9. Maintenance
Regardless of the used platform, every automation system needs routine maintenance, e.g. to have control over hardware and software updates, to replace faulty elements. An important advantage of PLC controllers is the ease of performing these activities in systems using PLC. Programs and configuration settings of any connected device can be sent to SD card in the PLC CPU slot, which greatly simplifies maintenance. Indeed, even if the PLC CPU itself is damaged, the new processor can be quickly inserted into the base board, and the original program loaded directly from the bootable version on the SD card, so that the system will start working immediately.
At the same time, we do not have to deal with the need for continuous firmware updates, which are the nightmare of PC-based systems, and we constantly worry that one update will conflict with another and will disrupt the entire system. From the perspective of industrial automation, the fact that PCs are multitasking systems is one of their greatest weaknesses.
10. Reduced IT requirements
One of the matters connected to the functionality of any automation system, which is important in integration between the plat floor and higher level systems, is the separation of duties between the automation engineering team and IT team. This can be a source of conflicts but we have to keep in mind that there will be almost inevitable lack of understanding from each about the requirements of the other.
In the case of automation systems using PLC controllers, the division of these tasks is clearly marked and there is rarely a need for an IT team to engage in work on the production line. What’s more, along with the availability of products such as the Mitsubishi MES module, which inserted into the base board of PLC provides a direct connection with higher-level databases – from automation systems you can completely remove entire layers of PC hardware, making the boundary between automation and IT even clearer.
SUMMARY
We can see that for many reasons PLC controllers will still be a pillar of control technology for automation systems. We have come to this conclusion without considering such issues as redundancy, security or the ability of modern PLCs to perform many complex mathematical functions that once were solely the domain of systems using PCs.Of course, the choice of the appropriate control system for given automation system should be made on the basis of substantive criteria, however, it should be noted that the PLC offers so many advantages that it should be treated as the first choice platform.